Control Module Power Circuit: Design Essentials
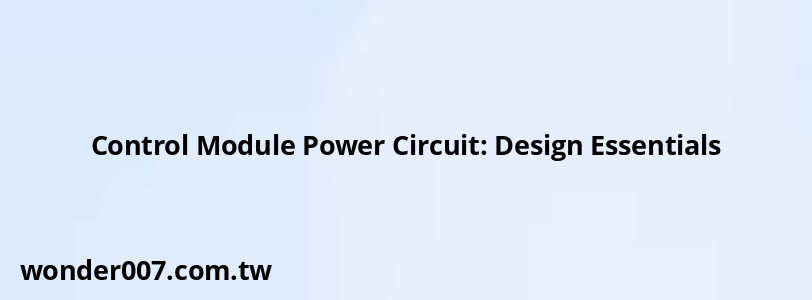
The control module power circuit is a critical component in electronic systems, providing regulated power to control modules that manage various functions. This circuit ensures stable and reliable operation of control systems across different applications.
Power Circuit Basics
A control module power circuit typically consists of several key components:
- Power source: Usually a DC voltage supply
- Voltage regulator: Maintains steady output voltage
- Filter capacitors: Smooth out voltage ripples
- Protection components: Fuses or circuit breakers for safety
- Isolation: Optocouplers or transformers for signal isolation
The design of these circuits requires careful consideration of voltage levels, current requirements, and noise suppression to ensure optimal performance of the control module.
Design Considerations
When designing a control module power circuit, engineers must address several crucial factors:
Voltage Regulation
Proper voltage regulation is essential for maintaining stable operation. Linear regulators are simple and low-noise but less efficient, while switching regulators offer higher efficiency but may introduce noise.
Current Capacity
The power circuit must supply sufficient current to meet the control module's demands. Overcurrent protection should be implemented to prevent damage from excessive current draw.
Noise Reduction
Electromagnetic interference (EMI) can disrupt control module operation. Techniques for noise reduction include:
- Proper grounding: Minimize ground loops
- Shielding: Protect sensitive components from EMI
- Decoupling capacitors: Place near ICs to filter high-frequency noise
Thermal Management
Power components generate heat, which can affect performance and reliability. Proper heat sinking and component placement are crucial for managing thermal issues.
Circuit Topology
The choice of circuit topology depends on the specific requirements of the control module. Common topologies include:
Topology | Advantages | Disadvantages |
---|---|---|
Linear Regulator | Low noise, simple design | Lower efficiency |
Buck Converter | High efficiency for step-down | More complex, potential EMI |
Boost Converter | Can increase voltage | Limited current output |
Testing and Validation
Thorough testing is crucial to ensure the power circuit meets all specifications. Key tests include:
- Load regulation: Verify stable output under varying loads
- Line regulation: Check output stability with input voltage changes
- Transient response: Assess circuit behavior during sudden load changes
- EMI testing: Measure and mitigate electromagnetic interference
Safety Considerations
Safety is paramount in power circuit design. Implement features such as:
- Overcurrent protection: Fuses or resettable fuses (PTC)
- Overvoltage protection: Zener diodes or dedicated ICs
- Reverse polarity protection: Diodes or MOSFETs
- Isolation: Where required by safety standards
Conclusion
Designing an effective control module power circuit requires a balance of electrical engineering principles, component selection, and careful layout considerations. By addressing voltage regulation, current capacity, noise reduction, and thermal management, engineers can create robust power circuits that ensure reliable operation of control modules across various applications.
FAQs About Control Module Power Circuits
- What is the main purpose of a control module power circuit?
To provide stable, regulated power to the control module, ensuring reliable operation and protection from electrical anomalies. - How do I choose between a linear and switching regulator?
Consider efficiency requirements, noise sensitivity, cost, and space constraints. Linear regulators are simpler and quieter, while switching regulators are more efficient but potentially noisier. - What are common causes of power circuit failures?
Overheating, voltage spikes, component degradation, and poor design leading to inadequate regulation or noise suppression are common causes of failure.
Related Posts
-
2000 Chevy Blazer Power Brake Booster Guide
26-01-2025 • 92 views -
OBD2 Port No Power: Troubleshooting Guide
29-01-2025 • 136 views -
How to Turn Off Speed Sensitive Volume Control in Your Car
29-01-2025 • 144 views -
1998 Toyota Camry Power Steering Pump: Essential Guide for Owners
28-01-2025 • 118 views -
Detroit Series 60: Troubleshooting Loss of Power Issues
29-01-2025 • 132 views
Latest Posts
-
Are O2 Sensors Covered Under Warranty
01-02-2025 • 282 views -
2015 Chevy Traverse AC Recharge Port Location
01-02-2025 • 295 views -
Power Steering Fluid Leak On Passenger Side
01-02-2025 • 328 views -
How To Turn Off Paddle Shifters Mercedes
01-02-2025 • 277 views -
Rear Brake Caliper Piston Won't Compress
01-02-2025 • 260 views
Popular Posts
-
2015 VW Passat Oil Consumption Issues Explained
26-01-2025 • 522 views -
EPC Warning Light: What It Means for Your Vehicle
27-01-2025 • 536 views -
V12 Engine Costs: What You Need to Know
26-01-2025 • 526 views -
EPC Light: Understanding Causes and Solutions
26-01-2025 • 885 views -
Power Steering and ABS Light On: Causes and Solutions
27-01-2025 • 474 views