Detroit Series 60 ECM Power Supply
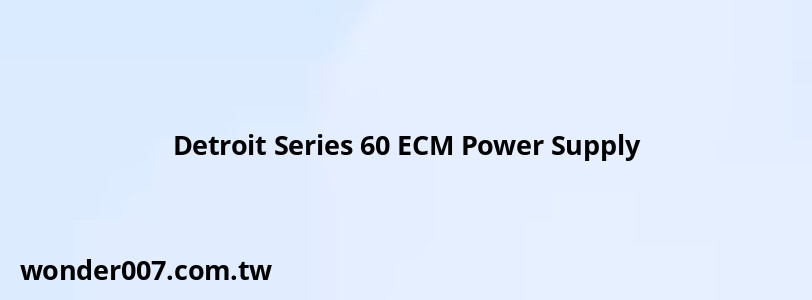
The Detroit Series 60 engine control module (ECM) power supply is a critical component that ensures proper functioning of the engine's electronic control systems. This power supply provides the necessary electrical energy for the ECM to monitor and control various engine parameters, including fuel injection timing, turbocharger boost pressure, and emissions control systems. Understanding the ECM power supply system is essential for diagnosing and resolving electrical issues in Detroit Series 60 engines.
The ECM power supply system consists of several key components, including the battery, alternator, wiring harness, and fuses. These components work together to provide a stable and reliable source of power to the ECM, allowing it to perform its functions accurately and consistently. Proper maintenance and troubleshooting of the ECM power supply system are crucial for ensuring optimal engine performance and preventing unexpected downtime.
Component | Function |
---|---|
Battery | Provides initial power and backup during engine operation |
Alternator | Generates electrical power while the engine is running |
Wiring Harness | Distributes power from the battery and alternator to the ECM |
Fuses | Protect the ECM and other electrical components from overcurrent |
ECM Power Supply Components
The Detroit Series 60 ECM power supply system relies on several key components to function properly. Each component plays a crucial role in ensuring that the ECM receives the correct voltage and current to operate effectively. Understanding these components and their functions is essential for maintaining and troubleshooting the ECM power supply system.
The battery is the primary source of power for the ECM when the engine is not running. It provides the initial surge of electricity needed to start the engine and powers the ECM during cranking. The battery also serves as a backup power source during engine operation, helping to stabilize the electrical system and provide power during periods of high electrical demand. For Detroit Series 60 engines, a 12-volt battery is typically used, although some applications may require a 24-volt system.
The alternator is responsible for generating electrical power while the engine is running. It converts mechanical energy from the engine into electrical energy, which is used to charge the battery and power the ECM and other electrical components. The alternator's output is regulated to maintain a consistent voltage, typically around 14 volts for a 12-volt system. Proper alternator function is critical for maintaining a stable power supply to the ECM during engine operation.
The wiring harness is a complex network of wires and connectors that distributes power from the battery and alternator to the ECM and other electrical components. The harness includes power wires, ground wires, and signal wires that carry information between the ECM and various sensors and actuators. The integrity of the wiring harness is crucial for ensuring proper ECM function, as damaged or corroded wires can lead to voltage drops, short circuits, or open circuits that can disrupt ECM operation.
Fuses are an essential component of the ECM power supply system, protecting the ECM and other electrical components from damage due to overcurrent conditions. The Detroit Series 60 ECM typically has multiple fuses dedicated to its power supply, including separate fuses for the main power feed and the keep-alive memory. These fuses are designed to blow if the current exceeds a safe level, preventing damage to the ECM and other sensitive components.ECM Power Supply Circuit Operation
The Detroit Series 60 ECM power supply circuit operates in a specific manner to ensure reliable and consistent power delivery to the ECM. Understanding how this circuit functions is crucial for diagnosing and resolving power-related issues that may affect ECM performance and engine operation.
When the ignition key is turned to the "ON" position, battery power is supplied to the ECM through a dedicated power wire. This initial power-up allows the ECM to perform self-diagnostics and prepare for engine start. The ECM also receives power through a separate keep-alive memory circuit, which maintains critical data such as fault codes and calibration information even when the ignition is off.
As the engine starts and begins running, the alternator takes over as the primary source of electrical power. The alternator's output is regulated to maintain a consistent voltage, typically around 14 volts for a 12-volt system. This regulated power is supplied to the ECM and other electrical components through the wiring harness. The battery acts as a buffer, helping to stabilize the electrical system and provide power during periods of high electrical demand.
The ECM constantly monitors its power supply voltage to ensure proper operation. If the voltage drops below a certain threshold, typically around 9 volts, the ECM may enter a low-voltage mode to protect itself and critical engine functions. In this mode, certain non-essential functions may be disabled to conserve power and prevent erratic operation.
The ECM power supply circuit also includes protection features to guard against voltage spikes and reverse polarity. These features help prevent damage to the ECM and other sensitive electronic components in the event of electrical system malfunctions or improper battery connections.
Troubleshooting ECM Power Supply Issues
Troubleshooting ECM power supply issues in Detroit Series 60 engines requires a systematic approach and attention to detail. Common symptoms of ECM power supply problems include engine no-start conditions, intermittent shutdowns, and erratic engine behavior. By following a structured diagnostic process, technicians can identify and resolve power-related issues efficiently.
The first step in troubleshooting ECM power supply issues is to check the battery voltage. Using a digital multimeter, measure the battery voltage at the battery terminals. A fully charged battery should read between 12.4 and 12.7 volts with the engine off. If the battery voltage is low, charge or replace the battery as necessary before proceeding with further diagnostics.
Next, inspect the wiring harness for signs of damage, corrosion, or loose connections. Pay particular attention to the main power and ground connections at the ECM. Loose or corroded connections can cause voltage drops and intermittent power issues. Clean any corroded terminals and ensure all connections are tight and secure.
Check the fuses in the ECM power supply circuit. Visually inspect the fuses for signs of damage or blown elements. If a fuse is blown, determine the cause of the overcurrent condition before replacing the fuse. Never replace a blown fuse with a higher-rated fuse, as this can lead to damage to the ECM or other components.
Measure the voltage drop across the main power and ground circuits to the ECM. With the engine running, the voltage drop should not exceed 0.5 volts on the power side or 0.2 volts on the ground side. Higher voltage drops indicate excessive resistance in the circuit, which can be caused by poor connections, damaged wires, or undersized conductors.
If all basic checks pass, consider using a diagnostic scan tool to communicate with the ECM and check for any stored fault codes related to power supply issues. Some ECMs have built-in voltage monitoring capabilities that can help identify intermittent power problems or voltage fluctuations.
Maintaining ECM Power Supply Reliability
Maintaining the reliability of the ECM power supply system is crucial for ensuring consistent engine performance and preventing unexpected downtime. By implementing a proactive maintenance strategy, fleet managers and technicians can minimize the risk of ECM power-related issues and extend the life of the engine's electronic control systems.
Regular battery maintenance is essential for ECM power supply reliability. Inspect batteries frequently for signs of corrosion, damage, or low electrolyte levels (in non-sealed batteries). Clean battery terminals and connections regularly to prevent voltage drops and ensure good electrical contact. Consider implementing a battery replacement schedule based on the manufacturer's recommendations and operating conditions.
The alternator should be inspected and tested periodically to ensure it is producing the correct voltage and current output. Check the alternator belt for proper tension and signs of wear. A slipping or worn belt can lead to reduced alternator output and potential ECM power supply issues. Replace the alternator belt at recommended intervals or if signs of wear are present.
Inspect the wiring harness regularly for signs of damage, chafing, or corrosion. Pay particular attention to areas where the harness may be exposed to heat, vibration, or potential damage from moving parts. Repair or replace damaged wiring promptly to prevent short circuits or open circuits that can affect ECM power supply.
Implement a preventive maintenance schedule that includes regular checks of the ECM power supply system. This should include voltage measurements, resistance checks of power and ground circuits, and inspection of fuses and connectors. Keep detailed records of maintenance activities and any issues encountered to help identify patterns or recurring problems.
Consider using advanced diagnostic tools to monitor ECM power supply performance over time. Some diagnostic systems can log voltage and current data, allowing technicians to identify intermittent issues or gradual degradation of the power supply system before they lead to major problems.
FAQs About Detroit Series 60 ECM Power Supply
- What voltage does the Detroit Series 60 ECM require?
The ECM typically requires a 12-volt power supply, with an operating range of 9-16 volts. - How can I test the ECM power supply circuit?
Use a digital multimeter to check battery voltage, measure voltage drops, and test continuity in power and ground circuits. - What causes ECM power supply failures?
Common causes include corroded connections, damaged wiring, faulty alternators, and blown fuses. - Can a weak battery cause ECM problems?
Yes, a weak battery can lead to low voltage conditions that may cause ECM malfunction or erratic engine behavior. - How often should the ECM power supply system be inspected?
Perform visual inspections during regular service intervals and conduct detailed checks at least annually or every 100,000 miles.
Related Posts
-
Electric Power Steering Warning Light: Troubleshooting Guide
30-01-2025 • 63 views -
How To Fix 2008 Mercury Mariner Power Steering Assist Fault
31-01-2025 • 84 views -
Power Steering Fluid for 2011 Ford Taurus: Essential Guide
29-01-2025 • 81 views -
Jeep Traction Control Light and Loss of Power
29-01-2025 • 85 views -
Power Steering Fluid for Acura TL: Essential Guide
29-01-2025 • 55 views
Latest Posts
-
2015 Chevy Traverse AC Recharge Port Location
01-02-2025 • 144 views -
Rear Brake Caliper Piston Won't Compress
01-02-2025 • 127 views -
Power Steering Fluid Leak On Passenger Side
01-02-2025 • 158 views -
Are O2 Sensors Covered Under Warranty
01-02-2025 • 132 views -
How To Turn Off Paddle Shifters Mercedes
01-02-2025 • 134 views
Popular Posts
-
2017 Ford Expedition Cabin Air Filter Guide
29-01-2025 • 219 views -
Cabin Air Filter: Essential Guide for 2009 Hyundai Elantra
29-01-2025 • 256 views -
Linde Forklift Warning Light Symbols Explained
26-01-2025 • 217 views -
Buick Verano: Years to Avoid for Buyers
26-01-2025 • 207 views -
PT Cruiser: Years to Avoid for Buyers
26-01-2025 • 294 views